|
|
HVAC |
HVAC
Machines> Italian Partner |
|
Best World Wide Italian Manufacturer
Letter of the manufacturer:
Our worldwide presence enables us to state that today
our machinery is working in over 50 countries
in the world, on the five continents. We strongly
believe that it is essential to constantly update
equipment and skills to respond to market demands. A
complete product range, high standard and reliability
are the main reasons why hundreds of clients have
decided to use our equipment.
We can offer a wide range of machinery
and special equipment.
Fin Lines,
Fin Presses,
Fin Dies,
Expanders,
Hairpin
benders,
return
bend and
sizing
machines,
Tube cut-off and
forming,
Brazing and
Welding lines. These
are just the most popular ones. Washing lines, Aluminum
Coating lines, Painting lines and others. Whatever the
client needs we try our utmost to offer.
|
General Machines
Fin
Press including Decoiler & Stacker
|
Fin Press |
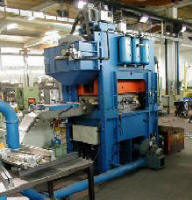
We designed our fin press in 1974. Since more than
25 years we are constantly upgrading and developing our
machines. The components, either mechanical, electronic,
pneumatic or hydraulic, are subjects of research and
development. Our aim is to offer the latest technology
and ensure reliability as well as performance.
Our presses aren’t just presses; they are fin presses.
It means that each detail has been carefully evaluated
in order to offer the best possible machine capable to
produce fins. The range includes 5 basic models and each
model at least three different versions as to tonnage
and configuration. Practically 15 different machines,
among them you can surely find the one closer to your
expectations and needs. In order to complete the
machine, you can select among several accessories,
evaluating with our engineers the best applicable
solution. Electronic control is made by using last
generation PLC, in this way further possibilities are
offered, such as diagnostics and dialogue with other
computers, either directly or by LAN.
We are really proud to be the European manufacturer who
has designed the first fin press and share our
satisfaction with all our clients who are using our
machine since many years. Their satisfaction spurs us to
continue in our job and bring to you all our capability.
Production line of special specifications can be made subject to
the user's requirements.
|
|
Fin Die
|
Fin
dies represent the most significant and outstanding part of our
technology. The experience in fin die manufacturing dates back
to the early 1950s. Since we designed our first die in 1972, we
have been working daily to improve and evolve. Thanks to new
materials and new manufacturing technology available. Thanks to
experience growing day by day, built on the field, acquiring
daily wider know-how and maintaining the market leadership. We
design is mainly a modular one. Each die unit is independent,
with independent die shoes, guides and columns. This peculiar
design ensures flexibility, precision and quick change over.
Available in several versions to satisfy different markets: air
conditioning, refrigeration, automotive. For each segment we
developed our technology and we can now offer our experience,
along with quality and reliability. Draw-less die, draw-type
die, special design for evaporative oil use, super slit louver,
v-waffled surface and more, all of them easy to adjust, easy to
maintain, easy to change. Materials used are subject of
research, in order to find the most appropriate one for every
requirement, combined with high level workmanship to be sure of
high precision. We do believe that only by investing and
concentrating all our efforts we can really offer what the
market is looking for. Our fin die is the guarantee of high
quality fins.
|
|
|
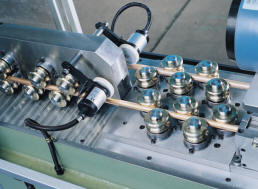
We
developed a range of machines capable to cut tube to length,
besides straightening and sizing it. It’s economically
convenient to buy tube wound in coils and cut it to length
as required in production. Our cut-off lines are suitable to
work copper, aluminum, cupro-nickel as well as other
materials. A wide range of tube diameters and thicknesses is
possible. Quick tool changeover, high production speed and
high precision in length and straightness. All machines are
controlled by a PLC and length set-up, as well as cycle
counting, is electronically performed. In addition we offers
special end forming, such as belling on the tube, always in
automatic mode. our cut-off line is one of our answers to
modern requirements.
|
|
Tube Bender (Hair Pin Bender)
|
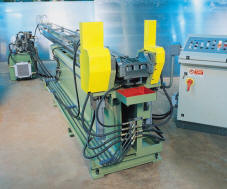
In any case of small production, and when hairpins are
used occasionally, it could be advisable to have a
semi-automatic machine, in order to satisfy specific
needs. The machine is fed with tubes cut to length and
performs tube bending, as well as the first length of
ejection, which is then to be completed manually, thus
apart from loading/unloading all other functions are
carried out automatically like on a normal automatic
machine. The machine is available in 3 basic models: 2,
4 or 6 tubes. All hairpins can have the same dimensions
(diameter and center-to-center), or else fully
individual dimensions. In this last case the machine
doesn’t require any tool change, reducing set-up time to
the minimum. Even the semi-automatic machine brings the
advantage of variable bending speed, and individual
micro lubrication, as well as a high level of controls
and quality of components. It offers the real innovative
solution in the field of hairpin bender machines. A new
and really innovative compact machine shape, to reduce
floor space without any loss in performance and quality.
As usual we focused our research on flexibility,
reliability and performance. We offers a wide range of
possible solutions as the first guarantee that our
semi-automatic hairpin bender machine is a really
customized machine.
|
|
Expander
Vertical, Horizontal, Portable
|
Expanding
of coils is one of the most diversified areas in coil
manufacturing. Huge variety in coil dimensions,
different tube materials, different tube thicknesses.
All matters creating the real individual type of each
requirement, each of these variables demanding a
different solution. This is the reason for us to explore
each market segment, locate the real need and study the
most suitable solution, one need one answer. We are
really proud to say that in our range almost any
application can find a proper method. Starting from a
single tube expander up to a multi-rod expander, 400
rods. Possibility to have a fully automatic control:
automatic height set-up as well as single rod selection.
On the multi-rod vertical expander, equipped with NC,
the set-up time has been reduced to less than 5 minutes,
offering the highest flexibility on the market. Special
care in design, along with high level of controls and
quality of components, offers the real innovative
solution in the field of expander machines. With the
horizontal expander we give the solution for the
expansion of stainless steel and other hard materials.
We offer different machine combinations, capable to
satisfy requirements in most production aspects. A new
and really innovative compact machine shape, to reduce
floor space and useless weight, without any loss in
performance and quality. As usual we focused our
research on flexibility, reliability and performance.
Easy to operate, easy to maintain. We offer a wide range
of possible solutions as the first guarantee that our
expander is a really customized machine.
|
|
Sizing & Ring insertion
Machine
|
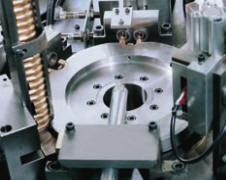
Machine designed for the sizing of return bends as to
tube roundness and center-to center, plus brazing ring
insertion: it is a complement of the return bend machine
as it slips the brazing rings onto the return bend, to
allow the further processing with the automatic brazing
machine. This model is the latest design, studied and
produced by the factory, aimed at offering the most
advanced technology. Special care has been taken to
reduce set-up time and to achieve easier and quicker
maintenance (with does not require any special skill).
The great flexibility reached, the complete equipment,
the optional list, the real reliability makes this model
one of the most advanced technical solutions to be used
in modern manufacturing processes. Sizing is
accomplished by means of two punches. Upon request the
machine can be equipped with a special unit to taper
both ends, for easier insertion into the tubes.
|
|
Blanking Machine
|
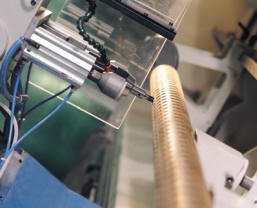
The blanking machine is devised for manifold production.
The material to be processed can be copper, steel or
other material on demand. It is offered in two basic
versions: automatic and automatic with NC control. No
mechanical difference, just a difference in machine
control. The NC version is equipped with a built-in or
peripheral computer, which results in easier and quicker
machine set-up. The operator merely needs to enter the
data identifying the manifold to be processed and the
machine automatically calculates the cycle. Another
advantage of the NC controlled machine is the
possibility to store production data for future use.
Available in three models: punching, drilling and
combined. In the latter version the machine is equipped
with a double working head. Specially designed for the
manufacture of coil manifolds, flexible and easy to use,
suitable for all production requirements, both for small
and large size coils.
|
|
|
For
years coil bending has been a problem solved by the
final client with different and sometimes empirical
methods. Now we can offer a machine suitable to this
purpose. This is the latest model studied and carried
out with the aim to offer the up-to-date technology, a
further proof that we are paying special attention to
all market needs and that it is engaged to find the
right solutions. With this kind of machine we have now
considerably reduced the risk to damage the coil, by
confining the operator’s action to coil loading and
unloading: all other operations are made in sequence and
automatically. The machine has been devised and equipped
with safety devices. The high versatility achieved the
complete standard equipment and the high reliability
makes this model one of the most advanced technical
solutions to be employed in modern manufacturing
processes. The coil bending machine has been studied to
perform coil bending both with L and U shape.
|
|
Automatic Assembling Machine
|
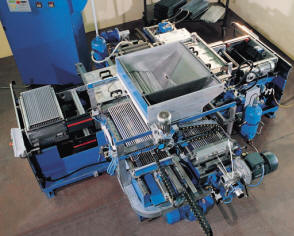
The new machine for automatic assembling of fin parcels
is specially designed for automotive application. It
includes 4 processing units: fin parcel loading station,
tube insertion station, expanding station, tube end
expansion station. The various processing steps will
take place simultaneously on all units. Floor to floor
time will thus be determined by the processing step that
requires the biggest amount of time (max. 1 minute). A
new pallet handling system, specially worked out by our
company, will cause any stress due to severe processing
to be absorbed directly by the machine frame and not by
the pallets, which would otherwise have to be reinforced
with steel plates, thus increasing their weight. The
first machine has been designed in 1990 and the latest
development, together with the demand to reduce
maintenance time and increase work safety, results in
the new design. It is a real solution for car radiator
production.
|
|
|
|
|